
Modular Homes | Prefab Houses | Resorts Hotels Building Construction | Wedge India
High Strength | Fireproof | Earthquake Proof | Long Life | Low Cost
Get best Modular homes construction, resort cabin, cottages, rooftop prefab hotel bar chalet farm house, garage, animal shelter dog cat shelter at wedge India. Buy low cost good quality Modular Home, Remote Office, Shelter for workers, Farm House, Studio, Prefabricated Buildings at Wedge India. Buy good quality panels and dry construction materials for making modular homes, farm houses, and prefabricated buildings. Manufacturing and supplying low cost prefabricated construction systems and modular building components timber frame, steel structure, aluminium profiles, cladding, partition, roofing, flooring, cement boards, sandwitch panels, insulation panels, precast concrete, staircases, walls, etc. Get best modular home low prices for sale at wedge india design house construction builders in Delhi Lucknow Gurgaon export studio.
Modular Homes
Modular homes, also known as prefabricated or prefab homes, are houses that are constructed off-site in sections or modules and then transported to the final location for assembly. These homes are built in a factory-controlled environment, ensuring higher quality control and faster construction times compared to traditional on-site building methods.
Here are some key points about modular homes:
-
Construction Process: Modular homes are built in sections or modules, which are typically manufactured in a factory using standardized designs and materials. These modules are then transported to the building site and assembled together to create the final home.
-
Customization: Despite the standardized construction process, modular homes can be highly customizable. Buyers can choose from various floor plans, architectural styles, and finishes to suit their preferences. The modules can be designed and combined to create a wide range of home sizes and layouts.
-
Quality and Durability: Because modular homes are built in a controlled factory environment, they often exhibit higher quality and durability compared to traditional stick-built homes. The factory construction allows for better precision and protection from weather elements during the building process.
-
Time and Cost Efficiency: Prefabricated homes can be constructed much faster than traditional homes since much of the building process occurs concurrently in the factory while site preparation takes place. The controlled environment and streamlined construction process also help reduce material waste and associated costs.
-
Transport and Assembly: Once the modules are built in the factory, they are transported to the final location using trucks or other means of transportation. On-site, a crane or similar equipment is used to lift and assemble the modules together. The assembly typically takes a few days to a few weeks, depending on the complexity of the design.
-
Building Codes and Standards: Modular homes must meet the same building codes and standards as traditional homes. They undergo inspections during the manufacturing process and on-site to ensure compliance with local regulations.
-
Affordability: Modular homes can offer a more affordable housing option compared to stick-built homes. The streamlined construction process, reduced labor costs, and economies of scale achieved in the factory setting can contribute to cost savings.
-
Mobility: One advantage of modular homes is their potential for mobility. Some modular homes are designed with the ability to be disassembled and relocated to another site if necessary. This feature can be advantageous for those who require flexibility or have temporary living arrangements.
It's worth noting that modular homes are different from mobile homes or manufactured homes. While mobile homes are built on a chassis with wheels and are designed to be mobile, modular homes are constructed in modules and are typically permanently affixed to a foundation.
Modular homes have gained popularity in recent years due to their cost-effectiveness, energy efficiency, and design flexibility. They offer an alternative option for homeowners who value quality construction, shorter build times, and customization choices.
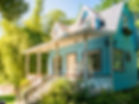
Prefab Houses
Prefab houses, also known as prefabricated houses or modular houses, are homes that are constructed off-site in sections or modules and then assembled at the final location. Prefabricated houses are built using a standardized and controlled construction process in a factory setting. They offer several advantages in terms of cost, time efficiency, and sustainability.
Here are some key points about prefab houses:
-
Construction Process: Prefab houses are built in sections or modules in a factory-controlled environment. These modules are constructed using standardized designs and materials. The construction process involves precise measurement, cutting, and assembly of the modules, which are then transported to the building site for final installation.
-
Design and Customization: Prefab houses offer a range of design options and customization possibilities. Buyers can choose from various floor plans, architectural styles, and finishes to suit their preferences. The modular construction allows for flexibility in adding or removing sections, creating different layouts, and customizing the interior and exterior design elements.
-
Time and Cost Efficiency: Prefabricated houses are known for their faster construction times compared to traditional on-site building methods. Since the modules are constructed in a factory while the site is being prepared, the overall construction process is more efficient. This can result in significant time and cost savings.
-
Quality and Durability: Prefab houses are built in a controlled factory environment, which ensures better quality control and adherence to building standards. The standardized construction process allows for precision in assembly and reduces the risk of errors. Moreover, the factory environment protects the materials from weather conditions, resulting in durable and long-lasting structures.
-
Sustainability: Prefabricated houses often prioritize sustainability in their design and construction. The controlled environment of the factory allows for better resource management, waste reduction, and recycling of materials. Additionally, the use of efficient insulation, energy-saving features, and sustainable building materials can contribute to the overall energy efficiency and environmental friendliness of prefab houses.
-
Transport and Assembly: Once the modules are built in the factory, they are transported to the building site for assembly. The modules are usually transported on flatbed trucks or shipping containers. On-site, the modules are lifted and assembled using cranes or other equipment. The assembly process is relatively quick, and the house can be ready for occupancy within a shorter timeframe compared to traditional construction.
-
Building Codes and Regulations: Prefabricated houses must comply with local building codes and regulations, just like traditional homes. They undergo inspections during the manufacturing process and on-site to ensure compliance with safety and quality standards.
-
Affordability: Prefab houses can offer a more affordable housing option compared to traditional stick-built homes. The streamlined construction process, reduced labor costs, and economies of scale achieved in the factory setting can contribute to cost savings. Additionally, the controlled construction environment helps minimize material waste and associated expenses.
Prefab houses have gained popularity due to their efficiency, sustainability, and design flexibility. They provide an alternative solution for homeowners looking for faster construction, cost-effective options, and customizable designs.

Price for Modular Prefab Homes
Pricing for 1100 SQF 2BHK prefab house | Type: Single storey house
-
Economic type : 14,00,000 INR
-
Standard type : 18,00,000 INR
-
Luxury type : 22,00,000 INR
-
Modern type : 23,00,000 INR
Inclusions: 1 living room + kitchen + 2 bedrooms + 1 bathroom + veranda
Walls, roof, windows, doors, floor tiles, kitchen and bathroom furniture, paints, electric and plumbing and all finishing are included. You only need to prepare a concrete basement for the house. If you request, we can also supply you steel floor structure and you can build the house on pillars.
​
Useful Information for Steel Prefabricated House Construction
-
Erection of the prefab house are easy and fast.
-
One 1100 Square Ft house can be built in 2 - 3 weeks.
-
No need Crane for erection
-
Wedge house packages include all materials.
-
You only need to prepare concrete foundation for the house.
-
We can produce and make the shipment of the house within 3 or 5 weeks.
-
You can send us your plan or we can design the plan.
-
We can dispatch the house by vessel or a truck to any city or country in the World.
-
We can customize technical specifications.
-
The materials have CE certificates and meet standards.
Modular & Prefab Building Materials
Buy good quality Modular and prefab building materials at Wedge India. These building materials designed for efficient construction processes, offering benefits such as reduced construction time, cost savings, and improved quality control. These materials are used in both residential and commercial buildings, allowing for various design possibilities and customization.
1. Structural Insulated Panels (SIPs): SIPs consist of an insulating foam core sandwiched between two structural facings, usually oriented strand board (OSB). They provide excellent thermal insulation and structural strength, making them ideal for walls, roofs, and floors in modular buildings.
2. Precast Concrete Panels: These are concrete panels cast in a factory setting and transported to the construction site for assembly. They offer durability, fire resistance, and sound insulation, and are often used for walls, floors, and roofs in commercial and industrial buildings.
3. Light Gauge Steel Framing: This involves using cold-formed steel sections to create a structural frame. It is lightweight, strong, and resistant to pests and fire, making it suitable for modular construction in both residential and commercial projects.
4. Timber Frame Panels: Prefabricated timber frames consist of wooden studs and beams that are pre-cut and assembled off-site. They provide a sustainable and renewable building option with high strength and versatility in design.
5. Cross-Laminated Timber (CLT): CLT panels are made by gluing layers of timber at right angles to each other, providing strength and stability. They are used for walls, floors, and roofs in modular construction, offering a sustainable and aesthetically pleasing option.
6. Prefabricated Roof Trusses: These are pre-engineered trusses made of wood or metal, designed to support the roof structure. They are manufactured off-site and delivered ready for installation, reducing construction time and labor costs.
7. Modular Wall Panels: These are prefinished wall panels that can be quickly assembled on-site. They come in various materials, including gypsum, metal, and composite panels, and are used for both interior and exterior applications.
8. Insulated Concrete Forms (ICFs): ICFs are hollow blocks or panels made of insulating foam that are stacked to form the shape of walls and filled with concrete. They provide excellent insulation and structural strength, making them suitable for energy-efficient buildings.
9. Prefabricated Bathrooms and Kitchens: These are complete bathroom or kitchen units that are manufactured off-site and installed as a single unit. They are fully fitted with plumbing, fixtures, and finishes, significantly reducing on-site construction time.
10. 3D-Printed Building Components: Advances in 3D printing technology allow for the creation of custom building components using various materials, including concrete and plastic. This technology is increasingly being used for modular construction, offering innovative design possibilities and rapid production.
These modular and prefab materials streamline the construction process, reduce waste, and often provide higher quality and performance compared to traditional construction methods. They are increasingly popular in various sectors, including residential, commercial, and industrial construction.